Mechamagnets
2018
Mechamagnets is an approach for rapidly prototyping haptic and functional physical interfaces through desktop 3D printing and embedded static magnets.
Through Mechamagnets, designers have an efficient means of detailing the physical form, function and haptics of physical interfaces. This is achieved with 3D printed parts with embedded magnets that move in a various degrees of freedom. The configuration of magnets enable different passive haptic responses. These same magnets also participate in the instrumentation of the physical interface with the help of linear Hall effect sensors.
︎︎︎GitHub
︎︎︎TEI 2018 ︎︎︎PDF
︎︎︎ TEI 2019 ︎︎︎PDF
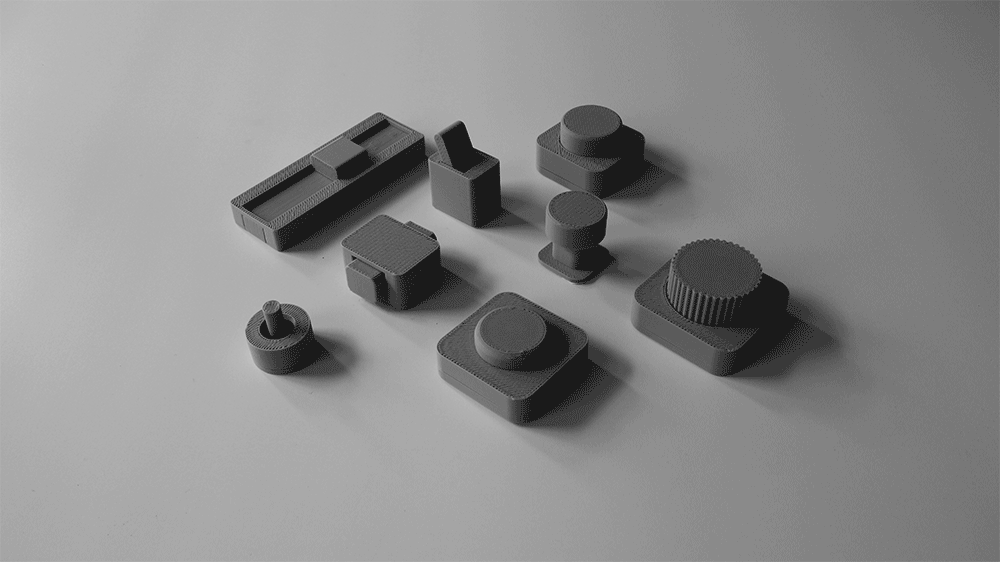
Tactile feedback with embedded magnets
+
Instrumentation with Hall effect sensors
+
Instrumentation with Hall effect sensors
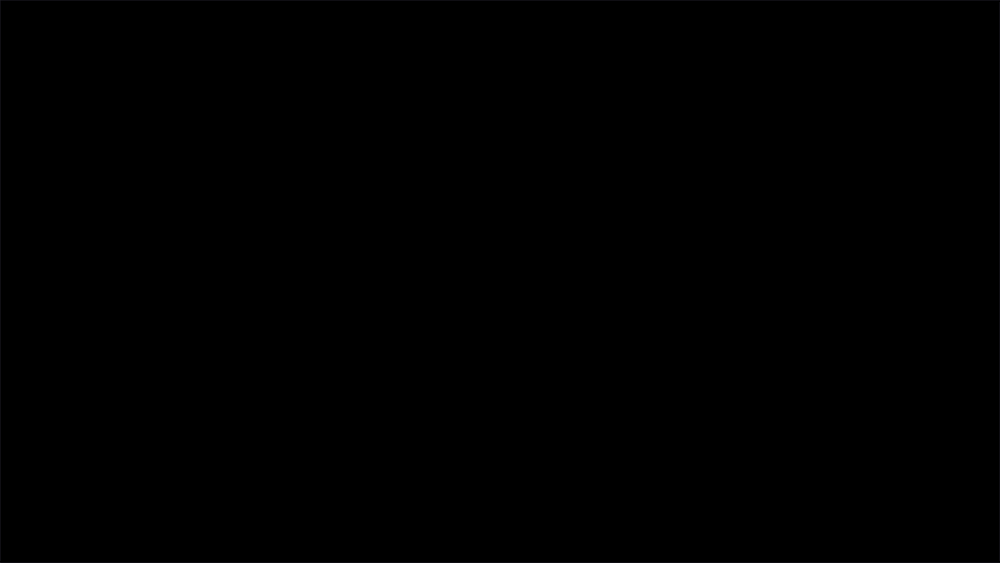
Exploring and fabricating haptic physical interfaces
Design to fabrication pipeline
Case study: creating a tangible input device
Case study: blending physical interactions
Case study: embedding haptic movements